Superlubricity coating could reduce economic losses from friction and wear Posted on 7 Jun 16:11
Superlubricity coating could reduce economic losses from friction and wear
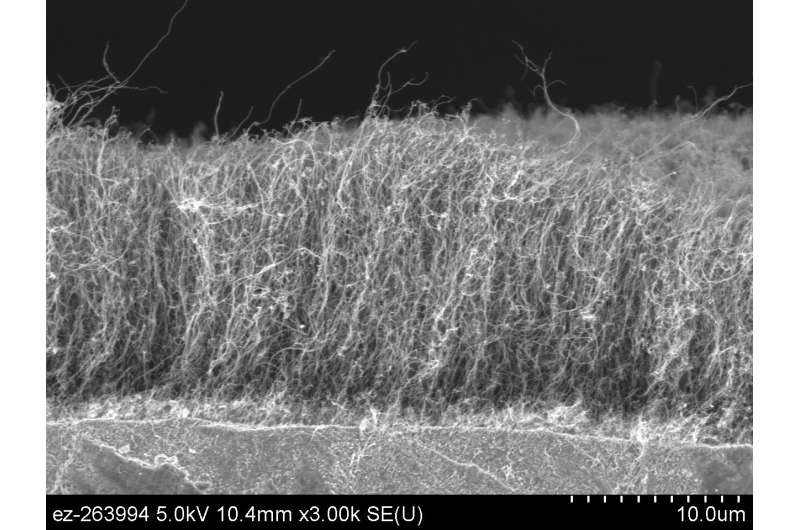
Scientists at the Department of Energy's Oak Ridge National Laboratory have invented a coating that could dramatically reduce friction in common load-bearing systems with moving parts, from vehicle drive trains to wind and hydroelectric turbines. It reduces the friction of steel rubbing on steel at least a hundredfold. The novel ORNL coating could help grease a U.S. economy that each year loses more than $1 trillion to friction and wear—equivalent to 5% of the gross national product.
"When components are sliding past each other, there's friction and wear," said Jun Qu, leader of ORNL's Surface Engineering and Tribology group. Tribology, from the Greek word for rubbing, is the science and technology of interacting surfaces in relative motion, such as gears and bearings. "If we reduce friction, we can reduce energy consumption. If we reduce wear, we can elongate the lifespan of the system for better durability and reliability."
With ORNL colleagues Chanaka Kumara and Michael Lance, Qu led a study published in Materials Today Nano about a coating composed of carbon nanotubes that imparts superlubricity to sliding parts. Superlubricity is the property of showing virtually no resistance to sliding; its hallmark is a coefficient of friction less than 0.01. In comparison, when dry metals slide past each other, the coefficient of friction is around 0.5. With an oil lubricant, the coefficient of friction falls to about 0.1. However, the ORNL coating reduced the coefficient of friction far below the cutoff for superlubricity, to as low as 0.001.
"Our main achievement is we make superlubricity feasible for the most common applications," Qu said. "Before, you'd only see it in either nanoscale or specialty environments."
For the study, Kumara grew carbon nanotubes on steel plates. With a machine called a tribometer, he and Qu made the plates rub against each other to generate carbon-nanotube shavings.
The multiwalled carbon nanotubes coat the steel, repel corrosive moisture, and function as a lubricant reservoir. When they are first deposited, the vertically aligned carbon nanotubes stand on the surface like blades of grass. When steel parts slide past each other, they essentially "cut the grass." Each blade is hollow but made of multiple layers of rolled graphene, an atomically thin sheet of carbon arranged in adjacent hexagons like chicken wire. The fractured carbon nanotube debris from the shaving is redeposited onto the contact surface, forming a graphene-rich tribofilm that reduces friction to nearly zero.
Making the carbon nanotubes is a multistep process. "First, we need to activate the steel surface to produce tiny structures, on the size scale of nanometers. Second, we need to provide a carbon source to grow the carbon nanotubes," Kumara said. He heated a stainless-steel disk to form metal-oxide particles on the surface. Then he used chemical vapor deposition to introduce carbon in the form of ethanol so that metal-oxide particles can stitch carbon there, atom by atom in the form of nanotubes.
-
A stainless-steel disk was heated to create iron and nickel oxide particles on its surface. The particles catalyzed carbon nanotube growth during chemical vapor deposition. Credit: Carlos Jones/ORNL, U.S. Dept. of Energy -
ORNL researchers used a tribometer for friction testing to show that carbon nanotubes in the presence of even one drop of oil could sustain superlubricity over 500,000 cycles. Credit: Carlos Jones/ORNL, U.S. Dept. of Energy
The new nanotubes do not provide superlubricity until they are damaged. "The carbon nanotubes are destroyed in the rubbing but become a new thing," Qu said. "The key part is those fractured carbon nanotubes are pieces of graphene. Those graphene pieces are smeared and connected to the contact area, becoming what we call tribofilm, a coating formed during the process. Then both contact surfaces are covered by some graphene-rich coating. Now, when they rub each other, it's graphene on graphene."
The presence of even one drop of oil is crucial to achieving superlubricity. "We tried it without oil; it didn't work," Qu said. "The reason is, without oil, friction removes the carbon nanotubes too aggressively. Then the tribofilm cannot form nicely or survive long. It's like an engine without oil. It smokes in a few minutes, whereas one with oil can easily run for years."
The ORNL coating's superior slipperiness has staying power. Superlubricity persisted in tests of more than 500,000 rubbing cycles. Kumara tested the performances for continuous sliding over three hours, then one day and later 12 days. "We still got superlubricity," he said. "It's stable."
Using electron microscopy, Kumara examined the mowed fragments to prove that tribological wear had severed the carbon nanotubes. To independently confirm that rubbing had shortened the nanotubes, ORNL co-author Lance used Raman spectroscopy, a technique that measures vibrational energy, which is related to the atomic bonding and crystal structure of a material.
"Tribology is a very old field, but modern science and engineering provided a new scientific approach to advance technology in this area," Qu said. "The fundamental understanding has been shallow until the last maybe 20 years, when tribology got a new life. More recently, scientists and engineers really came together to use the more advanced material characterization technologies—that's an ORNL strength. Tribology is very multidisciplinary. No one is an expert in everything. Therefore, in tribology, the key to success is collaboration."
He added, "Somewhere, you can find a scientist with expertise in carbon nanotubes, a scientist with expertise in tribology, a scientist with expertise in materials characterization. But they are isolated. Here at ORNL, we are together."
-
Chanaka Kumara of ORNL used a chemical vapor deposition system, in the background, to coat a stainless-steel disc, in the foreground, with carbon nanotubes. Credit: Carlos Jones/ORNL, U.S. Dept. of Energy -
Jun Qu of ORNL shows stainless-steel disks before (silver) and after (black) coating with carbon nanotubes that provide superlubricity. Credit: Carlos Jones/ORNL, U.S. Dept. of Energy
ORNL's tribology teams have done award-winning work that has attracted industrial partnerships and licensing. In 2014, an ionic anti-wear additive for fuel-efficient engine lubricants, developed by ORNL, General Motors, Shell Global Solutions and Lubrizol, won an R&D 100 award. ORNL's collaborators were Qu, Huimin Luo, Sheng Dai, Peter Blau, Todd Toops, Brian West and Bruce Bunting.
Similarly, the work described in the current paper was a finalist for an R&D 100 award in 2020. The researchers have applied for a patent of their novel superlubricity coating.
"Next, we hope to partner with industry to write a joint proposal to DOE to test, mature and license the technology," Qu said. "In a decade we'd like to see improved high-performance vehicles and power plants with less energy lost to friction and wear."
More information: Chanaka Kumara et al, Macroscale superlubricity by a sacrificial carbon nanotube coating, Materials Today Nano (2022). DOI: 10.1016/j.mtnano.2022.100297
Provided by Oak Ridge National Laboratory